MoldMaking Technology Noteworthy News, Apr. 22, 2021
The latest technology from BIG KAISER Precision Tooling, Siemens Digital Industries Software, and Kurt Manufacturing Company
Angle Head Line Accommodates All Machine Tool and CNC Machining Centers
Angle head line from Heimatec offers standard and custom styles for all tapers, including HSK and BT30.

Photo Credit: Heimatec
Heimatec announces the availability of its line of standard and custom angle heads, obtainable in a range of sizes and styles to accommodate machine tools and CNC machining center builders. Heimatec products are offered in North America by Platinum Tooling Technologies Inc.
Designed for heavy milling, deep drilling and tapping operations, Heimatec angle heads are made from high-tensile-strength aluminum. They feature twin or double-twin sets of matched angular contact bearings, plus a rear radial support bearing, ensuring maximum stability in use. All gears have inclined teeth made from high-resistance gear steel and have been hardened, ground and lapped in sets to provide smooth transmission output. High-precision spindle bearings maintain optimal spindle concentricity.
The angle head line additionally offers full 360º body rotation with positive compression locking, 90º incremental repositioning without indicating, maximum torque to 150 Nm and gear ratio 1:1 standard with others available. Spindle speeds up to 18,000 rpm and interchangeable torque arms are other standard features.
CAT 40, BT 40, BT 30, HSK 63A, CAT 50, BT 50 and HSK 100A taper styles are available, as well as custom modifications such at 18” extension shafts. Offset, Slim, Dual and Adjustable are other style options. Heimatec offers a full one-year warranty on all parts and labor.
Chip Blower Compatible with Hydraulic and Milling Chucks
The Big Kaiser Chip Blower has an extended steel shank for increased compatibility and can be used with automatic tool changers and programmed into a machining cycle.
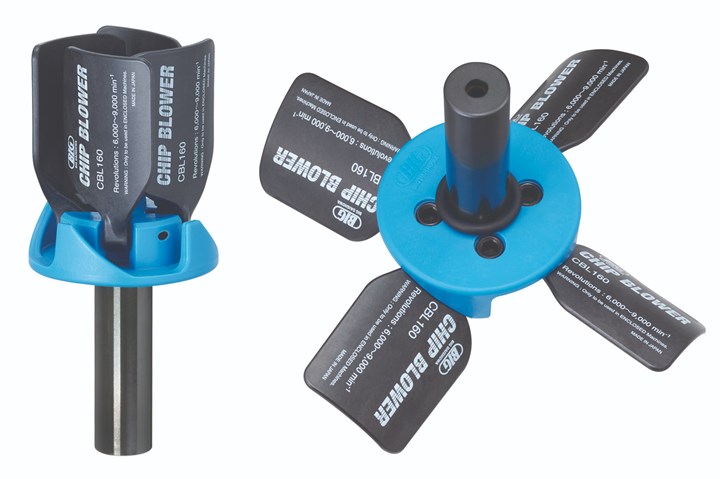
Photo Credit: Big Kaiser
Big Kaiser Precision Tooling has updated its Chip Blowers offering, which are designed to make removing chips and coolant from parts and machine tables fast, easy and safe. The new Chip Blower has an extended steel shank, from 1.77" to 2.5", for added compatibility with hydraulic and milling chucks.
The Chip Blower automates in-machine cleaning of coolant and chips by delivering high-volume air flow with spindle rotation. When not in use, the Chip Blower fits easily into any automatic tool change system for vertical, horizontal or multi-tasking machining centers. Big Kaiser says the Chip Blower can be used with automatic tool changers and programmed into a machining cycle, helping to improve machine utilization and increase productivity. The Chip Blower complements the solid construction, fixed blade ChipFan.
The Chip Blower is available with three blade length options and has center-through coolant capability for high-pressure washing.
Pre-Defined System Packages Offer Most Frequently Used CNC, Drive, Motor and Accessories
The Siemens Fast Track Program ensures fast and efficient delivery in less than 10 business days for U.S. customers, as well as a price discount.

Photo Credit: Siemens Digital Industries Software
Siemens Digital Industries Software is now offering pre-defined system packages that include what the company says are the the most frequently used Sinumerik 828D CNC, Sinamics drive, Simotics motor and accessories (such as cables), with fast and efficient delivery in less than 10 business days.
Ordering these pre-defined packages also include a price discount, a simplified ordering process and a shortened lead-time. The program is subject to availability and delivery time will depend upon the stock available at the company’s Elk Grove Village, Illinois, facility. Only customers located in the U.S. with a physical mailing and delivery address are eligible for this program.
There are seven pre-defined Sinumerik 828D packages covering the most typical standard milling and turning machines. They include:
- 3+1 Milling with 6.5-Nm feed axes and a 10-kW spindle
- 3+1 Milling with 12-Nm feed axes and a 22-kW flange mount spindle
- 3+1 Milling with 12-Nm feed axes and a 22-kW foot mount spindle
- Milling with three 12-Nm feed axes, no spindle with S120 Combi drive
- Milling with three 12-Nm feed axes, no spindle with S120 Booksize drive
- Turning with 3 6.5-Nm feed axes, no spindle with S120 Booksize drive
- Turning 2+1, 12-Nm feed axes and a 10-kW spindle.
Intelligent Lifting Point Achieves Greater Load Weights
RUD ACP-TURNADO bolt diameters are offered in a range of new sizes for load weights up to 16 tons, expanding its application range.

All photo credit: RUD
Lifting and lashing technology supplier RUD Ketten Rieger & Dietz GmbH u. Co. KG has launched new variants of the RUD ACP-TURNADO to achieve heavier loads up to 16 tons for higher working load limits (WLLs) and expand its application range. The intelligent-centric lifting point automatically rotates in the load direction when the load is lifted, preventing the lift bail from coming to a dangerous standstill and avoiding other associated high shear forces. This eliminates sagging and sudden reversal of the suspension bail, and enables a higher level of safety when handling load, crane and load-handling equipment.
Hermann Kolb, divisional manager of Sling & Lashing Units at RUD says the RUD ACP-TURNADO eliminates two known weaknesses of conventional centric lifting points, regardless of the size variant. For example, if a conventional lifting point’s U-bar stops in the “worst-case position” — when the lifting point is installed 90° from the side — it is exposed to large shear forces and bending moments. This can result in damage or breakage; as soon as the bracket then turns out of this position, the load usually sags.
RUD ACP-TURNADO incorporates a spring mechanism to prevent a 90-degree position of the lift bail, Kolb says, by turning it in the direction of the optimal split force introduction before lifting. Further, the company notes that unlike previous versions, the RUD ACP-TURNADO’s new, larger bolt sizes, come with the spring mechanism located internally, protecting against pollution.

In addition to safety-relevant aspects, the RUD ACP-TURNADO also offers handling advantages. Like the sizes M12 to M30, the large versions have a swivel joint in the U-axis as well as an exchangeable combination head bolt with internal and external hexagon, which enables optimum handling. Moreover, instead of a standard thread length across several sizes, an adapted thread length is available for each dimension. Wear lenses located at critical points of the lift bail are said to make it easy to assess whether the lifting point has already reached discard maturity.
A new feature, the deflector disc, offers an angle marking, to ensure users can estimate the applied lifting angle faster and easier. Additionally, the WLL specification in “t” and “lbs,” the safety factors 4:1 and 5:1 and the torque moment are pressed onto the disc, fulfilling American standard ASME B30.26 requirements.
RUD ACP-TURNADO, previously applicable for moldmaking, tool making, automotive, mechanical engineering, as well as the energy and offshore wind industries, is now qualified for applications where safety, high WLL and the need for improved handling are top priority. New bolt diameters M12 / ½”, M16 / 5/8”, M20 / ¾”, M24 / 1”, M30 / 1 ¼” as well as M36, M42, 1 ½” and 1 ¾” are available; RUD says other sizes from M48 to M100 are to follow shortly. An RFID transponder to simplify equipment checks is also serially installed, a procedure that reportedly reduces inspection costs, times and leads. Lifting operators can choose to manage inspection data and documents in their own databases or use Aye-D.Net software, a cloud-based equipment management tool offered by Syfit, a partner company of RUD.
Robotic Arm Gripper Achieves Automated, Quick-Change Design
The RV36 Gripper improves efficiency with quick-change, customizable jaws and custom accessories.

Photo Credit: Kurt Workholding
Kurt Workholding, a division of Kurt Manufacturing, launches the RV36 Robotic Gripper, a two-finger parallel gripper featuring a patent pending design that enables automated finger/end-effector changes without changing the gripper body itself via pull-stud technology. Quick-change jaws are said to help customers save on gripper-body expenses and create greater part-holding flexibility.
The compact Kurt RV36 Gripper comes standard with integrated electronics featuring sensors that ensure fingers and parts are in place and ready for production. High-strength aluminum alloy keeps gripper weight to a minimum while a hard-coat finish reduces wear and increases life in the field. Smaller gripper size aids in easier storage where space is a premium.
Further, the Gripper’s double-acting piston allows for maximum clamping and unclamping force. Customers can choose from carvable aluminum or steel finger options that can be machined to work in a variety of applications. Additional finger sets are also sold separately.
Read Next
How to Use Strategic Planning Tools, Data to Manage the Human Side of Business
Q&A with Marion Wells, MMT EAB member and founder of Human Asset Management.
Read MoreReasons to Use Fiber Lasers for Mold Cleaning
Fiber lasers offer a simplicity, speed, control and portability, minimizing mold cleaning risks.
Read MoreHow to Use Continuing Education to Remain Competitive in Moldmaking
Continued training helps moldmakers make tooling decisions and properly use the latest cutting tool to efficiently machine high-quality molds.
Read More