3D-Printed Stainless Steel Vent Pins Produce Defect-Free, Injection-Molded Parts
The Innovent Pin from Next Chapter Manufacturing is said to offer 10-15 times the volume of venting over traditional venting methods with suitability for filled and unfilled plastic resin grades.
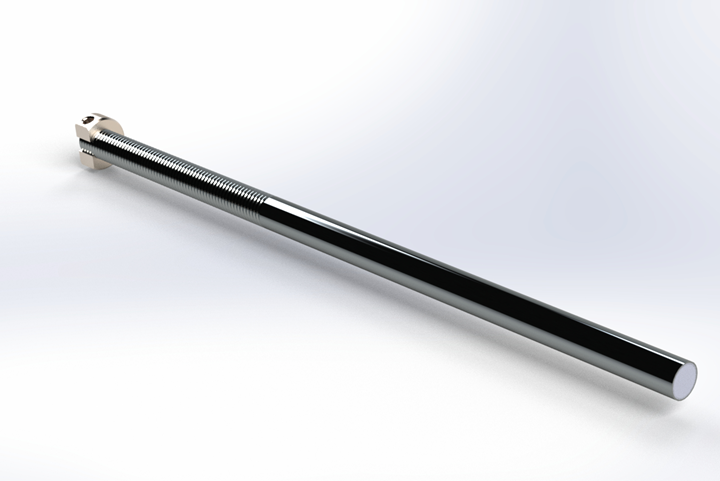
Photo Credit: Next Chapter Manufacturing
Next Chapter Manufacturing offers its Innovent technology in a standard component, the Innovent Pin, to eliminate the costly issue of gas traps in molds, which often lead to high scrap levels, cracking and weak parts. This design is made from 420 stainless steel to ensure no corrosion, produced via metal 3D printing and ground to exacting tolerances for a proper fit. A full, dense outer surface ensures smooth fit and crisp edges and an integrated porous core (20-30 microns) enables gas to pass through the face of the pin and vent out to atmosphere, producing high-quality, defect-free injection-molded parts.
According to Next Chapter, its pins offer 10-15 times the volume of venting over traditional venting methods and act as a drop in replacement for industry-standard pin sizes in 4″, 6″ and 11″ lengths. These pins are suitable for all typical filled and unfilled grades of plastic resin.
Place the pins in the area where a gas trap or burning is present on plastic parts to enable the gas to exhaust out efficiently. These can also be placed at end of fill under the part to provide venting where parting line vents can become blocked or coined over. Placing these under a screw boss or the bottom of a rib are common plastic part features that are critical areas for plastic to be of highest integrity. Custom sizes are available by sending CAD model to hello@nxcmfg.com.
Related Content
-
6 Ways to Optimize High-Feed Milling
High-feed milling can significantly outweigh potential reliability challenges. Consider these six strategies in order to make high-feed milling successful for your business.
-
Maintaining a Wire EDM Machine
To achieve the ultimate capability and level of productivity from your wire EDM on a consistent, repeatable and reliable basis, regular maintenance is a required task.
-
Treatment and Disposal of Used Metalworking Fluids
With greater emphasis on fluid longevity and fluid recycling, it is important to remember that water-based metalworking fluids are “consumable” and have a finite life.