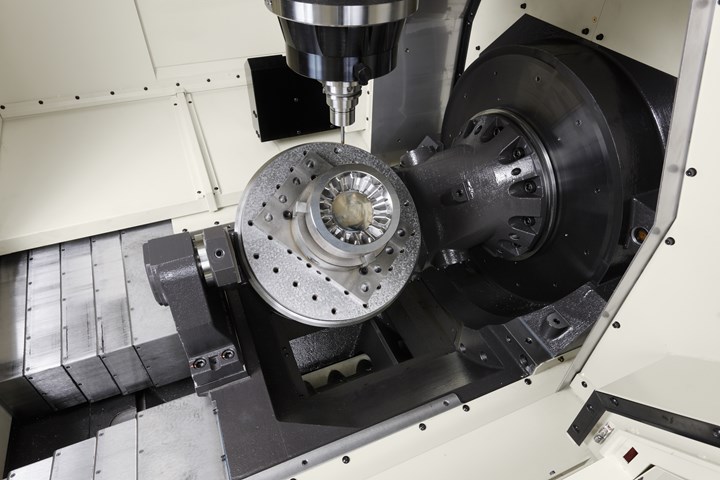
Five-axis machining gives mold builders the ability to work on five sides of a workpiece, which increases the time a mold is in the machine, minimizing human error and reducing production time. Photo Credit: Methods Machine Tools.
Mold manufacturing is an increasingly challenging industry. Whether you have pivoted to supplying the medical industry or are a longtime automotive mold/die producer, you have probably seen where the market is heading.
Parts and designs are getting more complex. Customers are pushing for shorter production times. Molds require greater degrees of precision and exact surface finishes. Switching from three- to five-axis machining may be the right solution for your business. Here are three key reasons why:
1. Reduce Your Costs
At first glance, you may have the misconception that five-axis machine tools are an exorbitant expense. But once you examine the bottom line, it's clear they can be a worthwhile investment that will lower your costs.
With the skilled labor pool continuing to evaporate, moldmakers are compelled to adopt automated solutions such as pallet changers and robotic loading. When a part has to be manually repositioned or transferred to another machine for secondary processes, your operational costs rise. Five-axis machines can further reduce manual intervention.
Five-axis machines are often capable of producing completed parts in just one or two operations, significantly reducing multiple setups, reapplying fixtures and manual intervention required with three-axis machining. Every reapplication of a fixture increases the chance for error and can add to the total cost of producing the component.
Lower costs are a common theme when transitioning from three- to five-axis machining. You may pay more for self-centering vises upfront, but it's a one-time cost. You're not going to need to buy costly, specialized fixtures later.
Additionally, the ability to work on five sides increases the amount of time the mold is in the machine, minimizing the chance of human error while reducing production time.
2. Maximize Efficiency
Three-axis machines can restrict your tool paths, tool choices and other critical manufacturing elements, ultimately holding you back.
Machining complex shapes, especially in mold and die making, can require long tools, tools with extensions and heat-shrink tools. One of the main benefits of five-axis machining is the ability to use shorter tools, translating to heavier cuts.
However, you don't need to machine complex shapes to realize the benefits of five-axis machining. With a more significant number of axes comes a greater number of choices. You can work with more tools and more tool paths, regardless of the shape.
3. Increase Precision
Additionally, five-axis machine tools allow for better relational accuracy. Tool center point control improves the finish of the workpiece surface while reducing machining time.
There are no downsides to switching from three- to five-axis machines. There are, however, some variables you need to consider before making the jump.
- What are you trying to accomplish?
- What type of machine could work for you?
- What are your specific needs?
With the right knowledge, support, and services, five-axis machine tools can help you excel rather than get by. Five-axis tool paths are a great tool to have in your tool bag when you're a moldmaker.
About the Authors
Ken Corklin has been working in manufacturing for more than 40 years. Ken has been with Methods Machine Tools for 14 years and has held various roles, from application engineer to the director of Channel Sales.
Kevin Lichtenberg has been working in the machine tool and automation industry for more than 30 years. He has had various titles throughout his career, including the president of two Wisconsin-based machine tool companies, and is currently the Yasda product manager at Methods Machine Tools.
Related Content
Five-Axis Graphite Mill With Automation Debottlenecks Electrode Machining
Five-axis electrode cutting enabled Preferred Tool to EDM complex internal screw geometry on an insert that otherwise would have had to be outsourced.
Read MoreMoldmakers Deserve a Total Production Solution
Stability, spindle speed and software are essential consideration for your moldmaking machine tool.
Read MoreDesign Strategy Tackles Big and Small Complexity Challenges for Southeastern Mold Builder
Delta Mold Inc.’s core values, engineering expertise, five-axis machines and molding capabilities help the team turn a proposal into a manufactured mold or part with custom design, finishing and assembly.
Read MoreTen Things You Need to Know about Circle Segment Milling
Considerations for evaluating if circle segment end mills or conical barrel cutters are right for your mold machining applications.
Read MoreRead Next
WEBINAR: How to Take Advantage of 3+2 and Simultaneous 5-Axis Machining to Increase Productivity
“First, think about what you are doing and why,” emphasized Ken Conklin, the director of the Methods Dealer Network for Methods Machine Tools, when he shared his advice on how to implement five-axis machining in mold manufacturing.
Read MoreHow to Use Continuing Education to Remain Competitive in Moldmaking
Continued training helps moldmakers make tooling decisions and properly use the latest cutting tool to efficiently machine high-quality molds.
Read MoreReasons to Use Fiber Lasers for Mold Cleaning
Fiber lasers offer a simplicity, speed, control and portability, minimizing mold cleaning risks.
Read More