2024 Outlook: Anticipating Trends and Opportunities for Mold Builders
The January 2024 issue lineup sets the tone for the variety of topics, technologies and trends that we will cover this year.
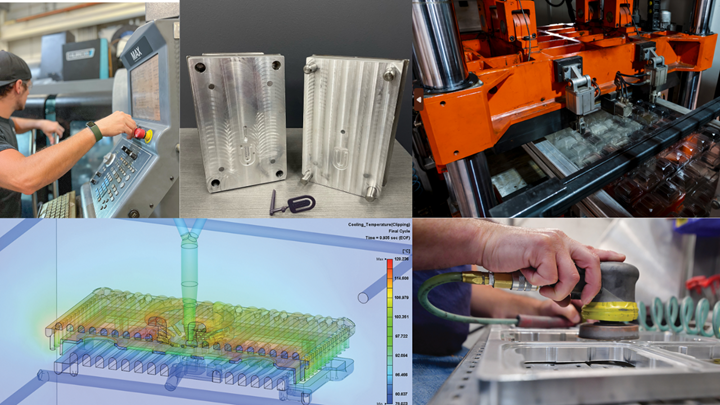
This issue’s lineup sets the tone for the variety of topics, technologies and trends that we will cover in 2024. Notably, the continuing impact of CAD/CAM on delivery times and lead time reduction, ensuring a rapid return on investment via features and functions that streamline processes and enhance design precision.
For software and surface treatment methods, we highlight the use of simulation for achieving a high-gloss surface finish. Moldmakers can predict and produce the exact surface finish required for high-gloss plastic parts through the strategic combination of simulation, conformal cooling, and a rapid heat and cooling process.
Data management and machining are crucial, emphasizing the pivotal role of remote machine monitoring. Real-time collection, analysis and secure handling of machine data are catalysts for substantial improvements in productivity, profitability and customer satisfaction.
The intersection of mold design and sustainability sees advancements that enhance material efficiency, employing a design for manufacturing approach and optimizing tooling design — such as adding ribs, flutes and structure — to boost packaging material efficiency.
Addressing hot runners, the industry aims to demystify benefits, improvements and everyday challenges based on decades of experience across various brands by simplifying the understanding of the hot runner and its function.
Robotics, simulation software and metal 3D printing can significantly reduce the labor required during the moldmaking process, allowing for shorter lead times and lower costs.
Speaking of labor, workforce development remains a key focus. We highlight collaborative initiatives between mold builders and educational institutions. A notable example involves a partnership that provides engineering and manufacturing students with hands-on moldmaking experiences covering the entire spectrum, from the design process to assembly and mold sampling.
We also continue to expand MMT’s editorial advisory board with the seasoned professional and president of a North Carolina mold shop who is passionate about high-speed machining, apprenticeship programs and the strategic growth of mold shops.
In this ever-changing, competitive industry, a commitment to innovation is required and remains evident. Through our ongoing profiles, we spotlight mold builders who, for example, use dedicated R&D facilities to pioneer new mold, machinery and automation technologies, staying at the forefront of high-precision mold manufacturing.
Moreover, due to reader feedback, fundamental principles are being brought back for a second look in a new series, From the MMT Archives. This month, it’s all about product data management within your CAD/CAM solution that can improve mold design and machining planning and processes.
As we begin the New Year, these emerging themes will influence the moldmaking community as it adapts to technological progress and a dedication to achieving excellence. If you have a topic that you’d like covered in MMT, reach out to me at cfuges@gardnerweb.com.
Related Content
-
Tackling a Mold Designer Shortage
Survey findings reveal a shortage of skilled mold designers and engineers in the moldmaking community, calling for intervention through educational programs and exploration of training alternatives while seeking input from those who have addressed the issue successfully.
-
Most-Viewed Content of 2022
The most popular MoldMaking Technology content according to analytics reports over the past 12 months.
-
Moldmaking is a Relentless Pursuit of Innovation
Innovation is at the root of mold manufacturing, which includes technology and strategies for mold design, automation, collaboration, communication, talent development, reshoring and sustainability.