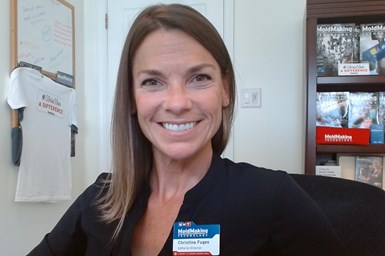
Source | MoldMaking Technology
As we put together our NPE 2024 Exhibitor Technology Showcase (see pages 38-55 of the April 2024 digital issue), we asked exhibitors to share the most significant trends they have observed since the last NPE in 2018. Following is a list of six trends that highlight the evolving nature of moldmaking and plastics:
1. Technological Advancements for Efficiency and Speed: There is a continuous drive for efficiency and speed to market, with companies offering comprehensive solutions to streamline processes and reduce downtime. For example, the use of ERP systems for integrated business management, 3D printing for cost-effective testing of new designs and improved cooling efficiency through conformal cooling, laser technology for 3D texturing, surface structuring, digital watermarking, electrification, digitization, and automation for repeatability and stability in both moldmaking and molding operations. This includes innovations in simulation, process monitoring, predictive maintenance, melt delivery systems, venting, high-temperature molding applications, mold changeovers and much more.
2. Education and Training: The industry continues to face a shortage of skilled labor. Companies are looking for ways to mitigate this challenge through automation, simplifying processes and improving ergonomics. There is an emphasis on training in CNC cutting, grinding, specialized grinding and EDM to help operators continually improve their skills. Educational institutions are adapting to industry needs, with courses focused on automation and hands-on experience in mold design and manufacturing. The industry is also adopting technological advancements like artificial intelligence (AI), machine learning and virtual reality in eLearning, providing personalized learning experiences and improving accessibility and inclusivity in training.
3. Vertical Integration: Mold builders are offering more services, including production molding capabilities and automation concepts in parallel with mold design to improve project timelines and address manufacturing issues early in the process.
4. Digital Transformation/Data-Driven Decisions: There is an increasing reliance on data-driven decisions to validate manufacturing strategies and make informed adjustments, not just on the production floor but in the toolroom as well. This trend requires using data to track and keep historical information on mold building and molding processes. Some key areas of development include AI, in-cavity sensors, mold monitoring and data security and ERP that integrates data from all aspects of the business — CRM, estimating, BOM, scheduling, accounting and HR. This also includes virtual meetings, video chats and digital data collection processes, which became even more important during the pandemic.
5. Part Complexity: Industries such as medical and electronics are requiring smaller and smaller parts and parts with more complexity, creating a need for smaller diameter core pins, including micro pins, and requiring innovative moldmaking techniques such as conformal cooling and new metal powders with higher thermal conductivity and toughness.
6. Sustainability and Environmental Responsibility: There is a growing focus on sustainability, leading to the development of eco-friendly materials, improved recycling technologies and more energy-efficient manufacturing methods. For example, biodegradable and bio-based plastics, increased demand for liquid silicone rubber products due to their bio-compatibility, heat and chemical resistance, hot runner systems and insulation and dry ice blasting for mold maintenance.
Related Content
Localized Mold Temperature Control Reduces Knit Lines, Optimizes Melt Flow
NPE2024: Dynamic localized mold temperature control Heat-Inject Technology by Incoe Corp. demonstrates how the part surface quality and the filling of the cavity is optimized with relatively little effort using targeted heat pulses.
Read MoreMold Builder Invests in Five-Axis Milling to Open the Envelope
NPE2024: Mold-Tech Inc., dedicated to complete quality and support, continues to add to its hard milling equipment department with the Makino D200Z, enhancing mold lead times, accuracy and efficiency.
Read MoreUnveiling the Future: Dive Into NPE2024's Moldmaking Marvels
Get ready for the ultimate moldmaking extravaganza! Explore exclusive previews of cutting-edge technologies and solutions shaping the industry at NPE: The Plastics Show.
Read MoreMagnetic Mold Clamping Amplifies Quick Mold Changes
NPE2024: Stäubli highlights its adaptable QMC123 technology, which is capable of calculating the clamping force for each mold beforehand, in addition to ensuring worker safety.
Read MoreRead Next
2024 Outlook: Anticipating Trends and Opportunities for Mold Builders
The January 2024 issue lineup sets the tone for the variety of topics, technologies and trends that we will cover this year.
Read MoreMMT Chats: A More Modern NPE “Made for You”
The Plastics Industry Association is making NPE 2024 a “can’t miss”’ experience with more of everything – education, exhibitors and networking! The PLASTICS Industry Association Chief Operating Officer Glenn Anderson and Director of Trade Show Marketing Damaris Piraino share what’s in store for attendees of next year’s May 6-10, 2024 in Orlando, Florida.
Read MoreAre You a Moldmaker Considering 3D Printing? Consider the 3D Printing Workshop at NPE2024
Presentations will cover 3D printing for mold tooling, material innovation, product development, bridge production and full-scale, high-volume additive manufacturing.
Read More