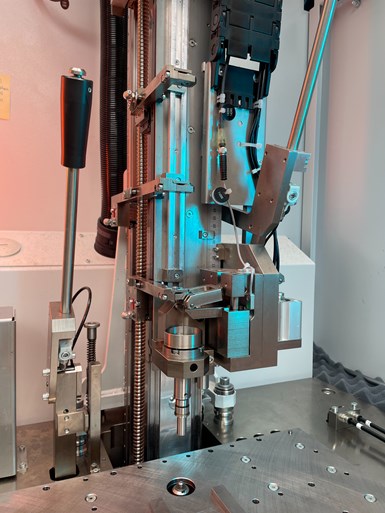
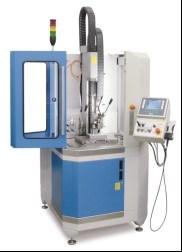
This precision honing system machines bores from 0.015 millimeter to 8 millimeters. Applications include hot runner nozzles, needle guides and ejector pin bores in injection molds. Photo Credit, all images: Microcut AG
Microcut honing technology is a user-friendly, economical solution for optimizing the function of small bores (diameters from 0.015 millimeter to 8 millimeters), especially for hard and difficult-to-machine materials. This technology enables the user to (a) produce the shape (roundness and cylindricity) and diameter within the narrowest tolerance ranges, (b) improve damaged surface structures (e.g., caused by spark erosion or hardening) via “cold” microchip machining and (c) compress the bore surface (inherent compressive stress).
The technology offers two significant advantages over conventional methods — milling, wire EDM and jig grinding — to machine needle guides and valve gates in hot runner systems:
1. A cost-effective, easily controllable process
The investment for a microcut honing machine is relatively small compared to conventional processing machines for bore machining. There is also savings potential in its ease of use because minimal training is required to operate the machine.
There is no need for time-consuming machine setup or tool dressing. Moreover, the machining process is robust and repeatable and the system requires minimal space (1 square meter) and energy consumption (2.5 volt-amps at 400 volts).
2. Quality
The critical tolerances for hot runner applications are diameter, roundness and surface roughness. For example, surface finish and roundness <0.001 millimeter must be achieved to yield diameter tolerances of 0.001 millimeter. The one-piece honing tools are pre-calibrated to the target diameter to reproduce these results without any problems.
Below are the tolerances microcut honing can achieve.
Microcut Honing Tolerance |
|
Diameter Range |
0.25 (0.01") – 8 mm (0.31") Bonded Grits |
Diameter tolerance |
±0.5 µm (0.00002") |
Roundness |
<0.2 µm (0.00001") |
Cylindricity |
< 1 µm (0.00004") |
Parallelism |
<0.4 µm (0.00002") |
Surface finish |
Rz: 0.5 µm (0.00002") (Ra: 0.05 µm) (0.000002") (N2) |
Cycle time |
Depends on the material, allowance, bore length |
Part geometries |
Rotationally and non-rotationally symmetrical |
Materials |
PCD, sapphire, ceramics, carbide, steel, powder metallurgical steel, various metal alloys, glass, various plastics |
Benefits for Needle Valve Nozzles
An important application in moldmaking is needle valve nozzles (Figure 1). The goal is to achieve an ideal sealing function between the needle and the needle valve nozzle (gate) with the needle still able to move. To respect that is a minimal defined mating clearance required. With the processing technology of microcut honing the best possible shape (roundness, cylindricity), surface and an exact dimension of the bore can be achieved.
Figure 1. Microcut honing improves the roundness, cylindricity, dimensional accuracy and surface roughness of this hot runner nozzle bore in a mold insert. Dimensions are in millimeters.
Figure 2 compares the roundness measurement of a jig ground or milled bore and a bore after microcut honing. Due to the geometrically precise bore with microcut honing, the diameter of the needle can be defined more accurately. This results in burr-free cast-on from the very first shot and an extended gate lifetime. Microcut honing can be used on new or existing molds to retrofit needle valve nozzles.
Figure 2. Jig ground or milled hole with roundness of 2.31 micrometers (left) and microcut honed hole with roundness of 0.16 micrometer (right).
Benefits for Needle Guides
The advantages of a very cylindrical bore with an optimized surface are also evident in needle guides with reduced wear on the needle and bore that enables the hot runner systems to be used on the machine for longer, reducing downtime and mold maintenance.
Unique innovative machining tools and the intelligent, force-sensitive control of the machining process offer an easily controllable and robust process with minimum dispersion. The actual machining is carried out with tools coated with diamond or CBN grit.
Microcut honing can precisely, efficiently and economically produce bores below 8 millimeters in diameter. The system, which can be configured in various sizes, offers advantages for bores with cross holes or clearances.
Related Content
Fundamentals of Designing the Optimal Cooling System
The right mold components can help improve mold cooling and thereby produce higher-quality parts.
Read MoreForces and Calculations Are Key to Sizing Core Pull Hydraulic Cylinders
To select the correct cylinder, consider both set and pull stroke positions and then calculate forces.
Read MoreMaintaining a Wire EDM Machine
To achieve the ultimate capability and level of productivity from your wire EDM on a consistent, repeatable and reliable basis, regular maintenance is a required task.
Read MoreMachining Center Spindles: What You Need to Know
Why and how to research spindle technology before purchasing a machining center.
Read MoreRead Next
Maintaining a Strong Relationship with Your Hot Runner Supplier
Once your hot runner supplier is chosen, you need to take the proper steps to maintain a mutually beneficial, long-term relationship.
Read MoreRevisiting Some Hot Runner Fundamentals
What exactly does a hot runner do? If you’ve been in the injection molding industry for any length of time, you might think the answer is obvious, but it is not.
Read MoreVIDEO: Hot Runner Maintenance Tips
Scott Clark, Hot Runner Business Manager for Husky Technologies, breaks down maintenance practices for hot runner systems.
Read More