How To Get Buy-In from Your Team for ISO 9001
Here are four tips for getting your team on board once you’ve decided to become ISO 9001 certified.
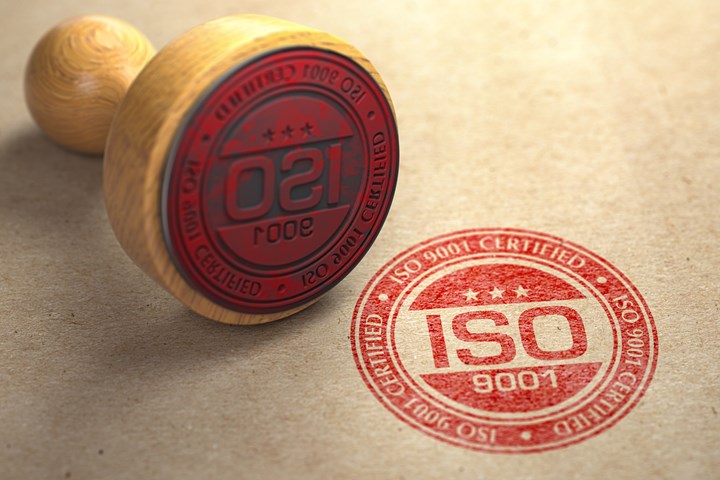
Photo Credit: Getty Images
You’ve decided to become ISO 9001 certified, or maybe you’re considering certification, but you still need to get your team on board. If your employees have experience with ISO 9001, they might have bad memories. Maybe they think of ISO 9001 as nothing but extra paperwork and one more burden in an already hectic schedule.
However, ISO 9001 doesn’t need to be any of those things. In fact, it can make life simpler — not just for your business but for your whole team. So how can you get your team on board with ISO 9001?
ISO 9001 Benefits Your Employees
ISO 9001 certification brings a wealth of benefits to your business. It makes you more competitive, increases customer satisfaction and bolsters your bottom line. But here’s what your team might not know: ISO 9001 doesn’t just benefit your company. It also helps your employees. So if you can convey the employee-focused benefits of ISO 9001, you can get your team to come along on the journey to certification.
Let’s look at four ways ISO 9001 benefits your team.
-
More Efficiency, Less Rework
There’s nothing worse than finishing a long, demanding job only to discover a significant mistake. We’ve all been there. But ISO 9001 cuts down on disruptions. It doesn’t add extra work on top of your already-busy processes. Instead, it streamlines those processes, defining them and optimizing them. And when problems do occur, ISO 9001 makes it easy to trace them to the source. This means fewer mistakes and fewer disruptions. With an ISO 9001 Quality Management System in place, your team can work hard without fear of needless rework.
-
More Growth, Less Grind
That increased efficiency also gives your business the ability to scale. A micro business with a handful of employees can often get by without much structure. But if you want to grow, you need processes that can scale up. This benefits your company. But how does this benefit your employees? Growth brings opportunities, both externally as more customers come to your door, and internally as positions expand and evolve. There’s also the pride that comes when your team sees growth due to their work. With ISO 9001, the same amount of work can go further than before; your team’s efforts are focused and unified on set objectives. They’re not grinding and getting nowhere. Instead, they’re part of something that’s going somewhere.
ISO 9001 certification involves everyone, from top management down. It lets your team take ownership of quality.
-
More Communication, Less Confusion
As a company expands, communication becomes more difficult. For example, you made decisions with three people at a conference table; now, those decisions involve multiple departments, maybe even multiple locations. Without consistent communication, a team can quickly grow confused or even frustrated. If you’ve ever found yourself in that situation, ISO can help. ISO 9001 also focuses on internal communication, from documenting the steps of a project to raising awareness of company policies. You can cut down on confusion, frustration and mistakes with consistent communication. ISO 9001 makes this a priority, and your team will feel the difference.
-
More Involvement, Less Frustration
ISO 9001 doesn’t just help you communicate to your team. It helps your team to communicate with you. Team members have a unique perspective. They work with your processes hands-on, and they can often identify the problems that top management might miss. If team members feel unable to express those problems, frustration quickly grows. But ISO 9001 empowers your team to voice these issues and fix them. ISO 9001 certification involves everyone, from top management down. It lets your team take ownership of quality. When appropriately implemented, it creates a “quality culture” where everyone at every level seeks to improve the business.
Related Content
Considerations for Mold Base Material Selection
Choosing the right material can greatly affect the profitability and cost of your application.
Read MoreHow to Correctly Size a Hydraulic Cylinder
This week Randy shares steps for correctly sizing a hydraulic cylinder on a mold.
Read MoreSurface Finish: Understanding Mold Surface Lingo
The correlation between the units of measure used to define mold surfaces is a commonly raised question. This article will lay these units of measure side by side in a conversion format so that companies can confidently understand with what they are dealing.
Read MoreMachining Center Spindles: What You Need to Know
Why and how to research spindle technology before purchasing a machining center.
Read MoreRead Next
Keeping Up with ISO: ISO 9001:2015 Certification Takeaways
One way to properly manage the moldmaking supply chain is to implement ISO guiding principles that govern every activity within a mold shop or molding facility.
Read MoreKeeping Up with ISO: The Value of Value Stream Mapping
Most people find it difficult to translate quality into in real dollars and cents.
Read MoreKeeping Up with ISO: Moving to ISO 9001:2015 Requires a Top-Down Approach
Implementing ISO guiding principles to govern every activity within a moldmaking or molding facility is essential to properly managing the supply chain. This new column will share knowledge, highlight opportunities and spotlight rewards of the ISO 9001: 2015 revision.
Read More