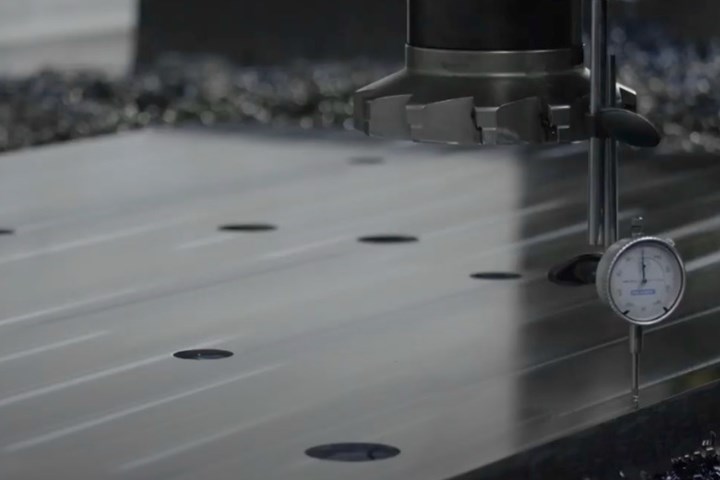
The patented micro-milling process1 can create flat, parallel plates that shorten mold build times. Imagine every plate being held within a couple thousandths regardless of size. Photo Credit: Steel 21.
Micro-milled1 steel plates are an ideal foundation for mold builders. A new, patented micro-milling process helps produce more accurate tools on the first run, ease components installation and limit rework.
On average, micro-milling can hold an A36/4140 steel plate three times more flat and parallel, and five times smoother than rotary surface grinding. The micro-milled plate can hold a 20-foot (240-inch) plate flat within 0.002 inches. In comparison, an average rotary surface-ground plate of this size would be out nearly 0.020 inches overall. This suggests that micro-milled plates can hold tolerances 10 times more flat and parallel on these large plates.
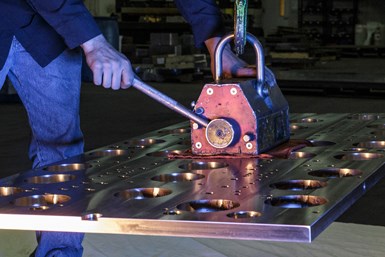
A magnetic system holds the steel and does not pull the warp out; it holds the steel in its dead state.
The memory of steel plays into machining accuracy, too. For example, rotary surface grinding creates friction heat by placing a large amount of rotating pressure on top of the steel. This forces the warp out of the plate only when pressure and friction are applied. Should the steel be released from the rotary surface grinder that was holding it in position, it will spring back to its ‘out-of-flat’ memory and may require numerous flips before reaching the industry standard of 0.001 inches per foot.
Micro-milling, on the other hand, machines the steel in its dead state. The process uses a magnetic self-leveling system that conforms to the bottom of the steel, so the steel can have a roll, twist or ripple to which the table will conform. The magnetic system holds the steel and does not pull the warp out of anything. It is simply holding the steel in its dead state.
With this process, the mill takes off the stock in a lot less time than a grinding wheel. Also, there is no friction heat, which eliminates another source of warping because this micro-milling process uses a cutting tool that moves across the steel, leaving the heat in the chip of the steel; you can put your hand on the steel as soon as the cutter passes because there is no warmth. In addition to not putting any friction heat into the steel, the process does not use any coolant either; it is a dry machining process.
Moreover, this process is fully recyclable, eliminating Blanchard grind sludge, which has been disposed in landfills since the 1900s.
Reference
1 21 Micro-milling is a patented machining process of Steel 21.
Related Content
How to Eliminate Chatter
Here are techniques commonly used to combat chatter and guidelines to establish a foundation for optimizing the moldmaking process.
Read MoreSolving Mold Alignment Problems with the Right Alignment Lock
Correct alignment lock selection can reduce maintenance costs and molding downtime, as well as increase part quality over the mold’s entire life.
Read MorePredictive Manufacturing Moves Mold Builder into Advanced Medical Component Manufacturing
From a hot rod hobby, medical molds and shop performance to technology extremes, key relationships and a growth strategy, it’s obvious details matter at Eden Tool.
Read MoreOEE Monitoring System Addresses Root Cause of Machine Downtime
Unique sensor and patent-pending algorithm of the Amper machine analytics system measures current draw to quickly and inexpensively inform manufacturers which machines are down and why.
Read MoreRead Next
How to Avoid Tool Steel Corrosion
A mold builder should consider corrosion resistance, hardness, machinability, processing, polishability, operational environment and wear resistance during tool steel selection.
Read MoreWelding Pre-hardened 40 Rockwell Material
Key tips help ensure safe shop welding practices when using pre-hardened 40 Rockwell material.
Read MoreMMT Chats: Working On and In an Apprenticeship Program
Four years later I follow up with two young moldmaking professionals who continue to help develop the apprenticeship program that got them to where they are today.
Read More