Modular Tooling Systems Enable Versatility in Hole-Drilling Operations
Sponsored ContentThe versatility of replaceable cutting edges offers users the ability to adapt to varied operations.
Share
The moldmaking industry presents some unique situations when it comes to drilling holes. There are a variety of hole types from simple threaded and clearance holes for capscrews to precision holes for guide pin and dowel pin alignments to deep and intersecting coolant channels. This necessitates a wide variety of drilling tool options. Sometimes mold makers need to revert to specialized machines in addition to the standard CNC machines.
These unique operations often require tailor-made tools. Manufacturers will revert to the traditional solid carbide drills and brazed head solid carbide gundrills for these operations. Resharpening is a common practice that requires dedicated grinding machines. There are still some applications that may require the traditional methods. But great advances have been made in modern, indexable tooling systems. The versatility of replaceable cutting edges offers modular system users the ability to adapt to varied operations. This helps to lower inventory levels, therefore reducing overall tooling costs. Additional labor costs can also be eliminated by doing away with resharpening equipment.
Simple Holes for Screw Threads
One of the most common holes produced in any industry is a threaded hole. Moldmaking requires many threaded fasteners to assemble an injection mold or die set. Whether the threads are machined by tap, threadmill or single-point lathe operation, a hole must precede the thread. Counterbores are often required for capscrew head clearances or spring pockets. Using a modular drilling system like ISCAR’s SumoCham replaceable head tools, allows you to drill a flat-bottom hole first by using a standard 90° head (FCP). The smaller through hole can then be drilled with a standard 140° head (ICP). This method is faster than drilling the small hole through the part then milling out the counterbore with circular interpolation. The varied geometries are all part of the same tool system. One common steel drill body will accept more than seven different interchangeable head geometries and a range of drill head diameters. Even the drill bodies come in various shank and drill depth combinations.
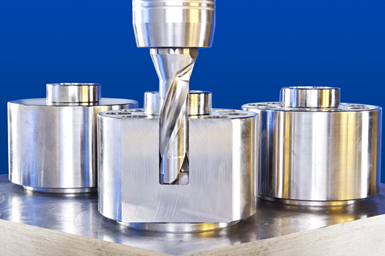
The Sumocham drilling family offers more than 12 drill head geometries for a variety of applications such as the FCP for a true 90° flat bottom hole. It will also work in breakout holes as shown.
When tap-drilling, sometimes a smaller hole will put excessive wear on the tap. With the Sumocham system, drill head diameters are offered in 0.1 mm (0.004 inch) increments. Exchanging a head to the next larger size will often keep the hole within tolerance, while slightly reducing the amount of material the tap engages. This may extend its life and avoid the frustration – and sometimes time-consuming endeavor – of extracting a broken tap from a workpiece.
Precision Holes for Alignment
For proper component alignment, a dowel pin, with a press fit into one component and a slip fit in the mating component, is used. These holes need precise location and diameter control to produce accurate mating surfaces. The common practice is to drill to create the hole; bore to hold the location; and ream to control the diameter. The new Logiq3Cham drill from ISCAR applies three cutting flutes to the process. Three points create a more accurate hole for diameter, circularity and cylindricity. The self-centering drill point holds a very tight, true position tolerance. This can make a boring operation obsolete. Depending on the target size, sometimes the reaming operation can also be eliminated.
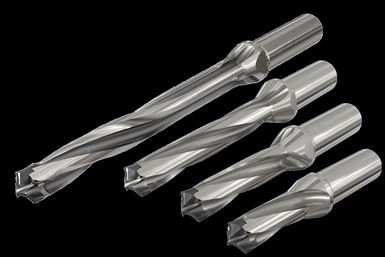
The Logiq3Cham drilling family offers four drilling depths from 1.5xD up to 8xD, and two cutting geometries. The additional cutting flute enables an increase in feedrate for reduced cycle time.
Deep Holes for Cooling
Moldmaking involves a lot of deep hole production using gundrills or BTA type solutions, and most holes are completed using gundrills with a brazed solid carbide head. Recent advancements for optimizing deep hole drilling involve the introduction of indexable gundrilling solutions. ISCAR offers two indexable lines, Tri-Deep and SumoGun.
Tri-Deep can provide extreme improvements in terms of penetration rates and overall productivity, as well as drastically reducing the cost of performing the same operation with a brazed-on solid carbide solution. Since it is a single flute design utilizing solid carbide guide pads, it can offer straightness rivaling the traditional gundrill. For intersecting holes, a second row of guide pads provide additional stability during the breakout and start of the hole on the other side. The Tri-Deep system covers holes from 10 to 32 mm in metric and 0.437 in. to 1.250 in. in common fractional inch sizes and for depths up to 2,400 mm (95 inches). Driver shanks are available for many of the dedicated gundrill machines as well as common mills and lathes.
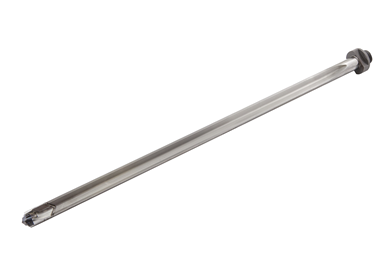
The SumoGun two-lip drill offers increased penetration rates compared to traditional brazed carbide gundrills. It also opens a variety of solutions with the versatility of the standard SumoCham head geometries.
If tighter diameter tolerance is required for a deep hole, then SumoGun, a two-lip drill, can offer increased penetration rates while offering the versatility and precision of the SumoCham line. Self-centering geometries and double margin heads help to improve straightness for the deep holes. The standard SumoCham line offers drill bodies up to 12xD drilling depth. Beyond that the SumoGun bodies in diameters from 10 mm (0.394 inch) to 25.9mm (1.020 inch), can reach from 200 mm (7.88 in.) to 400 mm (15.75 in.) with standard tools. Depths to 800mm (31.50 inches) can be made upon request.
Modularity Equals Cost Saving Solutions
Moldmakers today have many options for economical, indexable solutions for their hole-making operations. These tools provide increased penetration rates for productivity gains. The versatility of the standard modular options can help reduce inventory costs and shorten the delivery times often associated with receiving special tools.
Find additional details on these modular tooling systems and other cutting tools on Iscar.com.